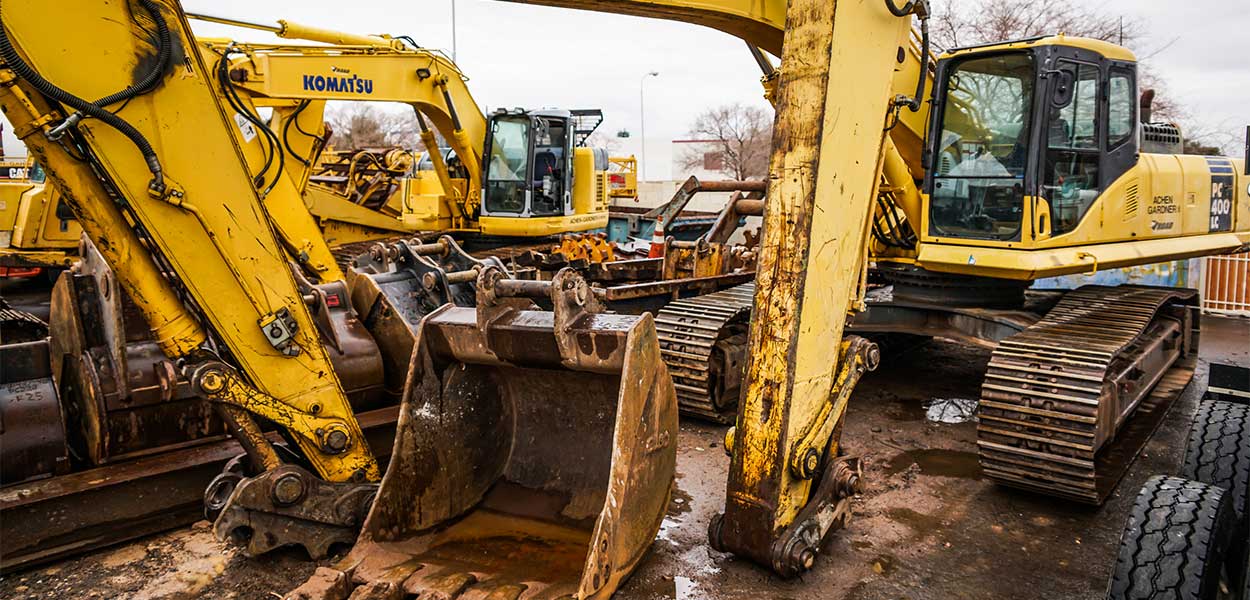
Over the years, I have managed or helped manage several different types of fleets, from military fleets to construction equipment. During that time, I discovered some essential skills and processes that have helped keep my equipment in good shape and my staff happy. Here are a few of those best practices that any construction equipment manager can utilize.
1. Have some mechanical comprehension. I was a full-time mechanic, both in the military and as a veteran, for about 15 years in some way or another, even while managing fleets. This helps a lot when you are talking to your mechanics or an outside vendor while explaining repairs and troubleshooting tasks that have been performed. With some basic mechanical knowledge, you also will have more confidence leading your team.
2. Do equipment market research. It is vital to know the current value of your equipment. Frequently check well-known auction websites for what similar equipment is actually selling for, not just what they are asking for it. Make sure to compare condition (as best as you can from a picture), hours, working environment, and age. I’d also recommend going to live auctions and taking notes on other equipment.
3. Be prepared for breakdowns. These happen at inopportune times and can get expensive if you’re not prepared. If you have your own repair facilities, make sure you know your inventory and scale that to your maintenance trends. If you don’t have your own maintenance facility, nail down guaranteed rates and agreements with the nearest vendors and OEM-certified repair facilities to get timely and quality repairs.
4. Have an inventory of parts. Whether or not you have your own repair facility, having an inventory of parts always is a good idea. When your prized paver goes down while laying asphalt and has three trucks waiting, you need to act fast, and it makes a big difference when your mechanic can leave the shop with the parts in his truck rather than having to order them. Even if you don’t have your own service personnel, it can make sense to keep some of those parts that have a long lead time in stock because you can always supply them for an outside service vendor that may not stock them.
5. Remember, time is money. This should go without saying, but I’ve seen people take too long to make decisions due to downtime or inefficiencies. In the shop, your team needs to have the right tools for the job to complete high-quality work in the shortest amount of time. You could be losing out on big money or early job completion bonuses due to indecision.
6. Have a backup plan. You may have enough equipment in your fleet to support your ongoing contracts, but what happens if multiple pieces go down in a short period of time? You will need a plan to get more equipment onsite from one of your yards. As a backup plan, have a written agreement with your local equipment rental companies. This could mean the difference between having to dispatch a field service crew to work all night or simply sending your lowboy driver with a pickup from your yard to finish the job.
7. Keep great records. Establishing and keeping a history is essential to equipment management. Tracking equipment usage history is very important when it comes to forecasting and seeing repair trends. For example, a paver’s screed plate will wear out faster if it operates in a region where the asphalt mix aggregate is harder. With that knowledge, you can forecast having to replace the plate based on the amount of material it ran through. Keeping repair records also helps you determine machine life cycle by showing why that piece of equipment failed and how much money you had put into it.
8. Stay organized. Having a mess in your office or in your truck doesn’t help anyone, especially you. We all have seen that person get out of their truck and a trail of papers or wrappers follow them. This is how vital documents and information are misplaced or forgotten. Software solutions help avoid maintaining a paper trail, so consider taking that route. In addition, I keep a small notebook on me at all times to help me track upcoming and completed tasks. However you decide to go about this, keeping all of your ducks in a row is key to effective equipment operations.
9. Work for your staff. I put a lot of emphasis on this because it is near and dear to my heart. When I was an non-commissioned officer (NCO) in the Marine Corps, my job was to lead the team and take care of them. To do that, I felt it was important to get to know each of my guys individually. I have taken this practice with me ever since my time in the military. A little effort to put yourself in someone else’s shoes can go a long way. Make it a priority to work for them as much as they work for you – a company is nothing without a good staff.
10. Enjoy your job. Equipment management is a fast-paced and unique job that brings something new every day. On any given day, you could deal with a number of different manufacturers’ equipment with different issues and different priority levels. And you have to make it all work together. This position isn’t for the faint of heart, but it is a career that you should be proud of since you’re helping to build our nation.
Do you have advice for fellow fleet managers or anyone in the equipment field? Let us know at marketing@hcss.com.
About the author
Dan Harvala has been in the equipment world since 2002. He helped maintain military and commercial equipment fleets while active in the US Marine Corps and as a civilian contractor for 14 years (4 years on active duty and 10 as a civilian contractor). Having worked globally in countries including Israel, Austria, Japan, Australia, and many more, Dan uses his broad cultural experiences to help other fleet managers make the right decisions. Dan currently manages equipment for Construction Resources Management, Inc., a major road construction and aggregate producer. He enjoys camping with his wife and two kids in Northern Michigan and practicing precision marksmanship.