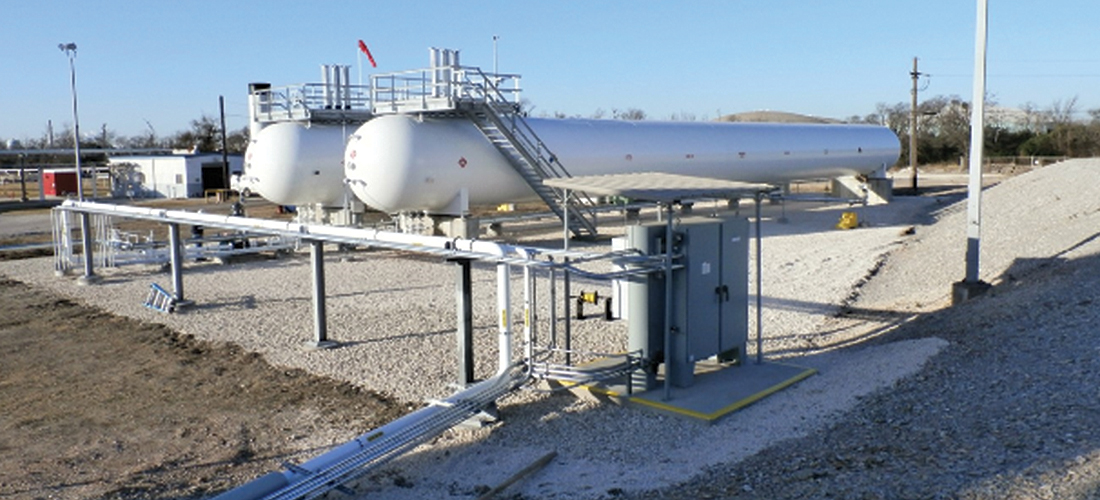
Sales is something safety professionals take for granted. We all have the picture of the well-dressed, overly aggressive smooth talker engrained in our minds. In reality, sales is something safety professionals do on a daily basis. We may not be selling widgets, but we are selling ideas and a culture. It is 2016 and we still work in a day and age where we have to periodically sell the idea of doing the right thing, doing the best thing, or doing the “safe” thing. While every day we continue to “sell safety” to our employees, selling safety has become a part of developing new business.
Just about every contractor in America is graded based on their historical safety performance. Lagging indicators such as EMR, previous 3-5 years of TRIR, and DART remain the grading scale of whether or not you are a “safe” contractor. I’m willing to bet that many of you weren’t even working for the same employer 3-5 years ago, but you are deemed either a safe or unsafe contractor based on information from that era. Competition for exemplary safety metrics is causing contractors to purposefully manipulate the data in order to remain in good standing with a customer. So, does a lagging indicator that can be so easily manipulated really tell you about a contractor’s safety culture? Absolutely not. Working safely is one thing, but having a good, engaging safety culture is another.
How We Overcame Our Safety Challenges
At XL Industrial Services, we work primarily in midstream oil/gas, performing mechanical, electrical, and abrasive blasting/coating within liquid gas terminal facilities. These terminals store gasoline and diesel fuel until it is transported to your favorite mini-mart so you can use in your vehicles. The industry can be tough. The demand for superior safety performance is through the roof, but then again, so are the dangers of working in close proximity to flammable materials. We also are a small company with around 65 employees. Our business takes us throughout the country, and we can have upward of 15 projects going on in 15 states at any given time. The hazards remain similar from project to project, as does the requirement to work safely.
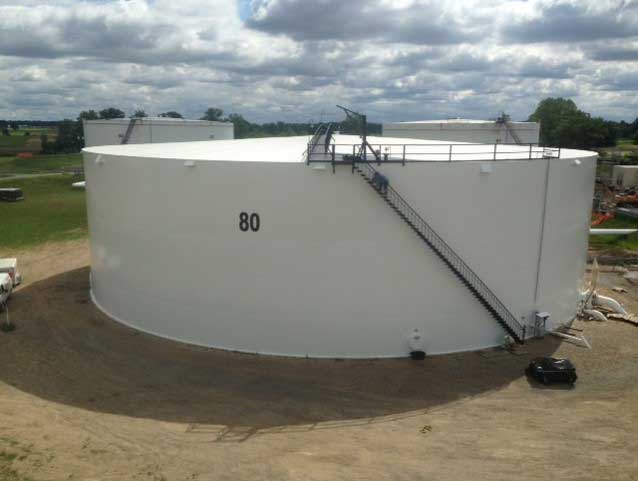
Our Business Development Manager, Steve Opdenaker, has always talked about safety when meeting with current or prospective customers and is prepared to address the same questions about our historical safety performance. While our historical safety performance is good, we needed to find ways to set ourselves apart from the competition. We needed to show off our safety culture in more ways than what has happened over the previous 3-5 years. Every day, our employees are responsible for completing and compiling so much safety-related information (e.g., JSAs, toolbox talks, equipment inspections, etc.), so how can we get the information across the country in real time in order to analyze active jobs for both detail and quality?
In June 2015, XL Industrial Services began using technology (specifically, HCSS Safety Manager) to help effectively manage our safety program anywhere in the country. This technology provides the real-time communication we were so desperately looking for. Foremen now can report a near miss or incident, submit an equipment or project inspection, conduct a toolbox talk or JSA, and send the documentation to management within seconds. This gives us the ability to track and trend field-related issues as they are identified as well as address needs or issues the same day. From June 1, 2015, to December 31, 2015, we have recorded:
• 1570 daily safety meetings (JSAs and toolbox talks)
• 1274 inspections conducted (1131 equipment inspections and 139 project inspections)
• 82 issues noted on all inspections
• 82 corrective actions tracked through completion
• Average corrective action closeout of 8 days
• Three near misses reported (zero reported from 2010 until implementation of the safety software)
Prior to 2015 and the implementation of technology, we didn’t have a way to track any of this information. We were extremely reactive, but then again, how could you not be? We now use all of this information to measure our performance. While I’m sure we’ve had more than three near misses in six months, the fact that our employees are using the software to report near misses is important to us.
“Our motto of ‘Safety First, Quality Always’ is real and meaningful for the entire company. In 2015 alone, XL Industrial Services invested nearly $100,000 in our employees’ safety, including the utilization of a state-of-the-art safety app. Foremen access the application with a company-issues iPad that instantly reports back to management anywhere in the country. At XL Industrial, ‘Safety First’ is real and we stand behind our employees and the safety program and its operation, with commitment from each and every employee.”
—Steve Opdenaker, Business Development Manager, XL Industrial Services
The ability to verify all of the information remotely and in real time has placed a lot of the ownership for safety activities on our field personnel. They know what they submit is being reviewed and in some cases shared with the customer they are working for. The attention to detail is drastically improved when they know they are being held accountable and that we are there to help address whatever caused the unsafe act to occur. Field personnel now are engaging the HSE manager on a daily basis to assist with needs onsite in order to close out a corrective action immediately instead of the information sitting around and not being properly reported.
Another impact, which is very important to us, is that safety is becoming fun. More and more of our employees are volunteering to complete our safety processes every day. They genuinely want to be part of something new and “cool.”
Positively Impacting Customer Relations
By using technology to most effectively manage our safety program, we now are able to share with both current and prospective customers what our field employees are doing about safety today, instead of what we did as a company last year. We went from lagging to leading, reactive to proactive. The ability to provide this information shows more than whether or not we are safe; it shows our culture and how important safety truly is to our company and our employees.
Word about our use of technology to assist in managing safety has spread within our customer base. Over the last 30 days, we’ve had a conference call and a meeting at the customer’s request to show them how this process works. They were able to see real-time data that they’ve never seen before from a contractor. These data are becoming a focal point in discussing new business opportunities with current and prospective customers. We’ve realized that customers, like our employees, think it’s “cool,” and who doesn’t want to be part of something cool?
About the author
Ryan Pollack is the Manager of HSE for XL Industrial Services, a full-service mechanical, electrical, and blasting/coating contractor that primarily serves midstream petrochemical companies, in addition to working in the industrial, chemical, and food processing industries across America. Ryan has worked in occupational safety for his entire career, serving the manufacturing, insurance, utility, and construction industries. He believes safety culture drives compliance and focuses on gaining trust with his workforce through building relationships since trust is the foundation from which all successful safety cultures are built. Ryan graduated from the University of Akron in 2006 with a BS in Emergency Management and AAS in Fire Protection. He also earned his CHST from the Board of Certified Safety Professionals in 2014.
Have an article that you would like to contribute? Click here to contact us.