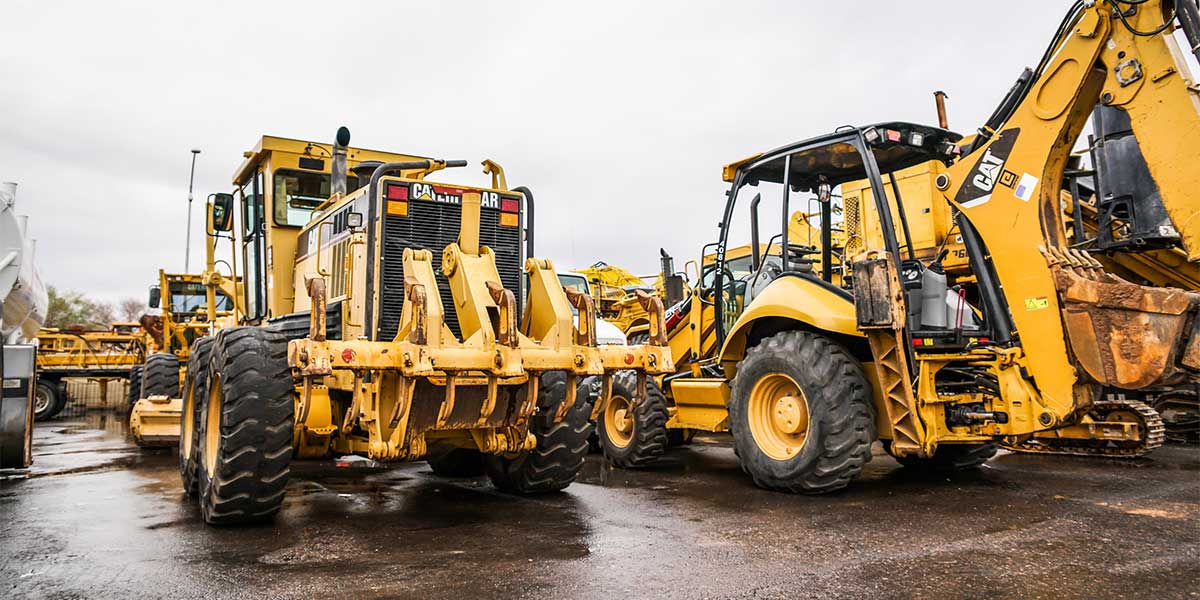
Whether it’s using Uber to get a ride across town or Waze to avoid traffic, our society is inundated with a million different ways to get any information at any time. Despite our familiarity with location technology and its nuances, many people think the term “GPS” refers to both the hardware and software of the system, when in reality, “GPS” is a reference to the location portion of the hardware capabilities, and telematics is the system which transmits location and other machine health data.
While we all know that GPS is an integral part of the telematics product, telematics is much more than just a latitude/longitude address. Is calling telematics “GPS” a subconscious indication of what most end users identify as the highest ROI-generating part of telematics? Or is it just a common jargon mistake? More importantly, is the lack of knowledge about telematics connectivity with support/services products preventing fleet managers from expanding to more than just asset location?
When those in the fleet industry talk about telematics, the discussion usually includes more than just GPS. While GPS is an integral piece of the machine information technology puzzle, it is only a small piece of the ROI telematics generates.
For example, government mandated environmental regulations forces manufacturers to use intelligent machines with new engine control technology for emissions compliance. These machines require OEM and distributor monitoring and support for the latest updates, maintenance for maximum uptime, operator training, and compliance. In addition, some of the new machines often cannot be maintained or repaired in-house. In these cases, remote diagnostics and monitoring is a viable solution that lends itself to quality improvements in machine and operator safety.
This solution provides many benefits including allowing for efficient monitoring and maintenance planning, measuring idle time and fuel consumption for competitive operation and governmental compliance, reviewing operational procedures and habits, making best practices a habit, and improving safety protocols.
Reducing idle time saves fuel and more importantly, leads to longer and more productive machine life cycles. Companies can reduce non-productive engine idle periods by utilizing warranty periods for actual work time. Reducing a machine’s idle time by at least 10% over the life of the unit can result in a significant increase in the machine’s selling value versus a comparable unit with 10% more idle hours. Machines once deemed too expensive to own and operate may now be considered for purchase, which gives owner a competitive edge over relying on outside resources and subcontractors.
Next time when the topic of how you can improve your fleet management process comes up, make sure to evaluate telematics technology for all its benefits, not just the latitude/longitude coordinates.
About the author
Daniel Samford CEM, principal of Peak Performance Asset Services LLC, consults in fleet management, mixed fleet telematics integration, negotiations for specialized construction equipment and annual vehicle purchases, national accounts, and fleet value evaluations. Previously with Herzog Companies for 21 years, Samford managed a fleet of over 2,800 units and 700 vehicles with a replacement cost of over 250 million dollars in operations throughout the continental U.S., Alaska, Canada, Mexico, Guam, and the Caribbean. He has been directly involved in equipment ownership and operating evaluations throughout his career. Samford sits on the AEMP Board of Directors, its Telematics Futures committee, and has been vocal on the need for a unified telematics language and single portal equipment management for the construction equipment industry. He can be contacted through his website www.PPASllc.com or at dsamford@PPASllc.com
Have an article that you would like to contribute? Click here to contact us.